植物由来の素材「CNF」をクルマに活用へ
自動車材料のエキスパートの挑戦に迫る植物由来の素材「CNF」をクルマに活用へ
自動車材料のエキスパートの挑戦に迫る
自動車材料のエキスパートの挑戦に迫る植物由来の素材「CNF」をクルマに活用へ
自動車材料のエキスパートの挑戦に迫る
2019.10.1
金沢工業大学高信頼ものづくり専攻の影山裕史教授は、環境省の国家プロジェクト「ナノ・セルロース・ビークル・プロジェクト」(Nano Cellulose Vehicle Project、以下「NCVプロジェクト」)に、副プロジェクトリーダーとして参画している。同プロジェクトは、植物由来の新素材として注目されるセルロースナノファイバー(以下「CNF」)を自動車に実装しようという世界初の試みだ。日本が世界に誇るフラッグシップ技術となる自動車へのCNF転用について、最前線で奮闘する影山教授に尋ねた。
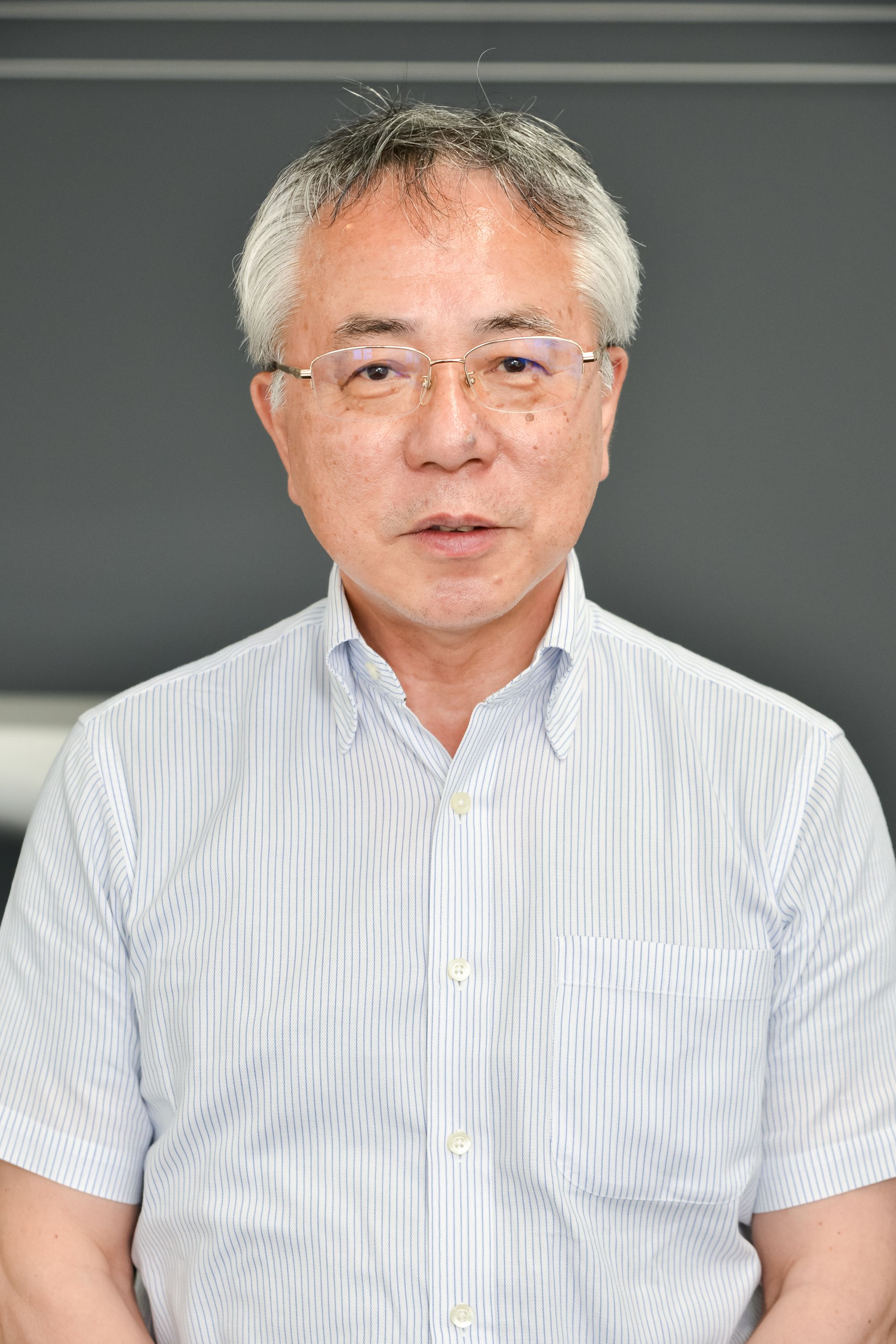
金沢工業大学
大学院工学研究科
高信頼ものづくり専攻 教授
影山 裕史 (かげやま ゆうじ)
東京工業大学有機材料工学科卒、同大学院有機材料工学修士課程修了。トヨタ自動車工業(株)(現:トヨタ自動車(株))入社。バイオプラスチックスやCFRP材料の研究開発を通して、レクサスLFAのCFRPボデーの量産などを手掛ける。2014年金沢工業大学教授。専門は自動車における複合材料(炭素繊維系、植物繊維系)の材料設計技術および成形技術。現在、環境省NCVプロジェクトのほか、NEDO「革新的新構造材料等研究開発」のサブプロジェクトリーダーや、経済産業省地域中核企業創出・支援事業のグローバル・コーディネーターなどを兼任。
大学院工学研究科
高信頼ものづくり専攻 教授
影山 裕史 (かげやま ゆうじ)
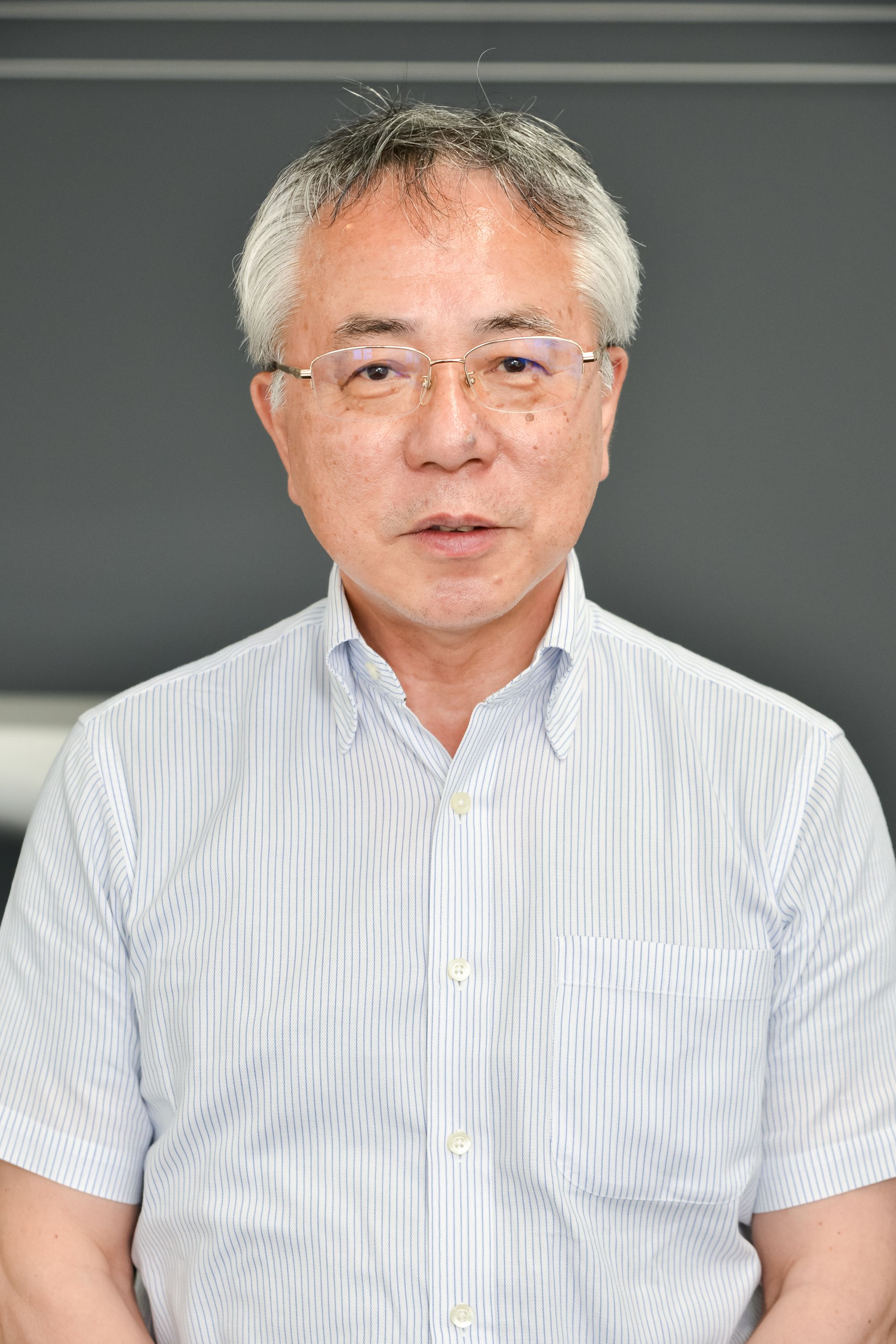
影山 裕史
(かげやま ゆうじ)
金沢工業大学
大学院工学研究科
高信頼ものづくり専攻 教授
(かげやま ゆうじ)
金沢工業大学
大学院工学研究科
高信頼ものづくり専攻 教授
東京工業大学有機材料工学科卒、同大学院有機材料工学修士課程修了。トヨタ自動車工業(株)(現:トヨタ自動車(株))入社。バイオプラスチックスやCFRP材料の研究開発を通して、レクサスLFAのCFRPボデーの量産などを手掛ける。2014年金沢工業大学教授。専門は自動車における複合材料(炭素繊維系、植物繊維系)の材料設計技術および成形技術。現在、環境省NCVプロジェクトのほか、NEDO「革新的新構造材料等研究開発」のサブプロジェクトリーダーや、経済産業省地域中核企業創出・支援事業のグローバル・コーディネーターなどを兼任。
ゼロ・エミッション達成に向けて
植物由来のCNFの可能性に期待
植物由来のCNFの可能性に期待
「CNFは植物由来の素材ですが、“ナノ”と名のつく通り、非常に細かい繊維です。これを樹脂の中に均一に入れ込んで自動車の部品として使用しようとしています。自動車業界では、環境を汚染し気候を混乱させる廃棄物の排出ゼロをめざす『ゼロ・エミッション』への取り組みが盛んです。その一環として、地球温暖化に繋がるCO2排出を抑制するため、CNFへの期待が高まっているのです。植物由来で、いわゆるカーボンニュートラルの原料ですから、ゼロ・エミッションに貢献します。しかも、軽量でありながら高い強度と弾性率を持つため、自動車部品には特に期待が大きいのです。カーボンニュートラルとは、植物のように育つときにCO2を吸収し、たとえ燃やしたとしても、その分のCO2を出すだけであり、CO2の出入りは±0である現象を意味しています。
CNFは、樹脂に15~20%ほど混入すれば、高い強度と弾性率が得られます。そのため、従来の射出成形法が使用できます。現状での課題の一つはコスト面です。パルプを微細な繊維にするために、細かく砕くのですが、この工程にかかるコストが高いのです。ただ、現状では高価でも、近い将来CNFのニーズが高まれば安くなると想定されます。おそらくは1㎏あたり500円以下のラインに下がると見込まれています。
他の課題は、木からつくるということで、燃えやすい=燃焼性、水を吸いやすい=吸水性、人体に悪影響のガス=VOC(揮発性有機化合物)が懸念されます。CNFを自動車に使った場合、特に夏場は車内が高温になるのでVOCが発生しやすくなりますね。今回、プロジェクトで燃焼性とVOCについて評価試験を行った結果、基準値を満たすデータが得られています。
CNFは、樹脂に15~20%ほど混入すれば、高い強度と弾性率が得られます。そのため、従来の射出成形法が使用できます。現状での課題の一つはコスト面です。パルプを微細な繊維にするために、細かく砕くのですが、この工程にかかるコストが高いのです。ただ、現状では高価でも、近い将来CNFのニーズが高まれば安くなると想定されます。おそらくは1㎏あたり500円以下のラインに下がると見込まれています。
他の課題は、木からつくるということで、燃えやすい=燃焼性、水を吸いやすい=吸水性、人体に悪影響のガス=VOC(揮発性有機化合物)が懸念されます。CNFを自動車に使った場合、特に夏場は車内が高温になるのでVOCが発生しやすくなりますね。今回、プロジェクトで燃焼性とVOCについて評価試験を行った結果、基準値を満たすデータが得られています。
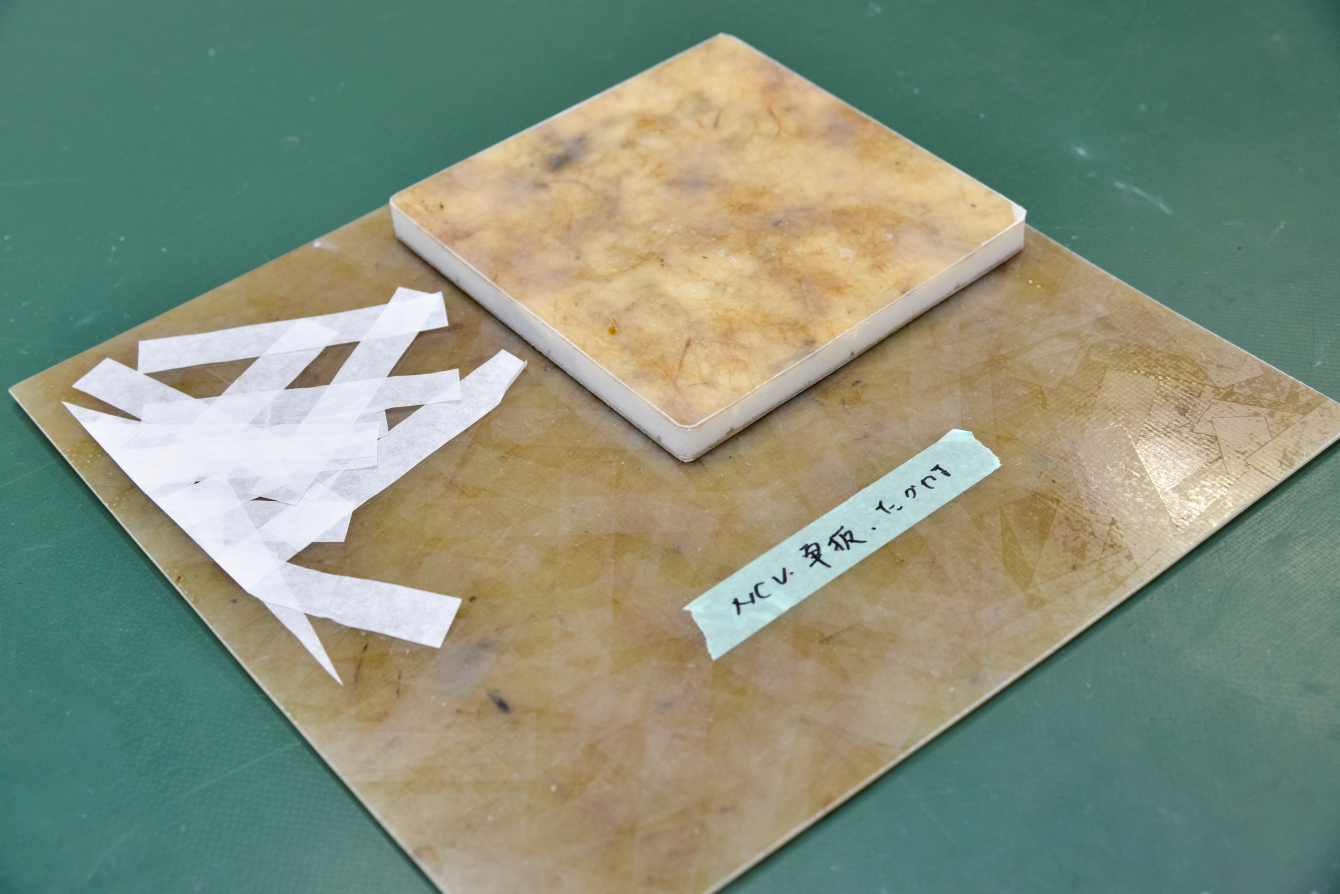
CNF(左の白い断片)を使って試作した自動車用の外板の一部
このCNFを使った部品を自動車に実装し、軽量化によるCO2削減をめざし性能評価・検証をしようというのが、NCVプロジェクトだ。現在、NCVプロジェクトでは内装材を中心に取り組んでいるが、本来は外板や骨格部材にもCNFを使うことが理想。これらの部品は自動車の中でも特に重い部類に入るからだ。
「外板や骨格にCNFを使うことができれば、自動車の総重量をかなり軽量化することが可能になります。そこで金沢工業大学が中心になってトライしているのが、エンジンフードです。CNFを実機に搭載することで、軽量化によるCO2削減効果等の性能評価と早期社会実装に向けた導入実証を行うことができます。プロジェクトは、京都大学が中心となっていますが、金沢工業大学をはじめ複数の大学と企業、研究機関が参画していて、私たちはエンジンフードへの実装を担当し、さらにはフロアにも挑戦しています。
私はかつてトヨタ自動車に在籍し、CFRP(炭素繊維複合材料)ボデーの開発に従事していました。CFRPの成形法として、RTM成形(Resin Transfer Molding)技術があります。同じ技術をCNFにも活用できないかということで取り組んでいます。現状ではなかなか好感触を得ており、今後に期待を持っています。
エンジンフードは鉄製、アルミ製をはじめ、CFRP製のものもあります。さまざまな面で比較しやすい部品であることから、まずはCNFでもこの部品からやってみようということになったのです」 CNFを自動車に使うことで、軽量化が促進でき燃費性能が改善され、ゼロ・エミッションの達成目標である「走行時のCO2排出量の低減」に貢献できることになる。
「電気自動車になると、走行時にCO2を排出しないので、環境面では軽量化はあまり意味がなくなってしまう。ただし、電気自動車でも燃費ならぬ“電費”面に軽量化は大きく寄与するので、やはり有用ということになります。
しかし、CO2排出の問題は走行時だけを想定しては不十分です。その素材を製造する際のCO2排出も考慮する必要があるのです。その点で、CFRPは製造時の排出量が問題視されます。アルミニウムも軽量ですが、製造時に電力を浪費するのでなかなか難しい。そうなると、軽量かつ植物由来で製造時の電力消費やCO2排出量が少なく、環境に優しいCNFこそが、来たるべき電動カー時代と2050年を見据えたゼロ・エミッションの実現に向けて期待される新素材だと言えるのです。ただ、CFRPも製造時のCO2排出量を削減できれば、まだまだ可能性を秘めていると思います。たとえば、CFRPならではの特性である異方性(物理的性質が方向によって異なること)を活かしてエンジンフードのフレームに、逆に等方性の特性を有するCNFをパネルとし、一体成形すれば理想的ですね。どちらの材料がいいということではなく、適材適所の発想です」
「外板や骨格にCNFを使うことができれば、自動車の総重量をかなり軽量化することが可能になります。そこで金沢工業大学が中心になってトライしているのが、エンジンフードです。CNFを実機に搭載することで、軽量化によるCO2削減効果等の性能評価と早期社会実装に向けた導入実証を行うことができます。プロジェクトは、京都大学が中心となっていますが、金沢工業大学をはじめ複数の大学と企業、研究機関が参画していて、私たちはエンジンフードへの実装を担当し、さらにはフロアにも挑戦しています。
私はかつてトヨタ自動車に在籍し、CFRP(炭素繊維複合材料)ボデーの開発に従事していました。CFRPの成形法として、RTM成形(Resin Transfer Molding)技術があります。同じ技術をCNFにも活用できないかということで取り組んでいます。現状ではなかなか好感触を得ており、今後に期待を持っています。
エンジンフードは鉄製、アルミ製をはじめ、CFRP製のものもあります。さまざまな面で比較しやすい部品であることから、まずはCNFでもこの部品からやってみようということになったのです」 CNFを自動車に使うことで、軽量化が促進でき燃費性能が改善され、ゼロ・エミッションの達成目標である「走行時のCO2排出量の低減」に貢献できることになる。
「電気自動車になると、走行時にCO2を排出しないので、環境面では軽量化はあまり意味がなくなってしまう。ただし、電気自動車でも燃費ならぬ“電費”面に軽量化は大きく寄与するので、やはり有用ということになります。
しかし、CO2排出の問題は走行時だけを想定しては不十分です。その素材を製造する際のCO2排出も考慮する必要があるのです。その点で、CFRPは製造時の排出量が問題視されます。アルミニウムも軽量ですが、製造時に電力を浪費するのでなかなか難しい。そうなると、軽量かつ植物由来で製造時の電力消費やCO2排出量が少なく、環境に優しいCNFこそが、来たるべき電動カー時代と2050年を見据えたゼロ・エミッションの実現に向けて期待される新素材だと言えるのです。ただ、CFRPも製造時のCO2排出量を削減できれば、まだまだ可能性を秘めていると思います。たとえば、CFRPならではの特性である異方性(物理的性質が方向によって異なること)を活かしてエンジンフードのフレームに、逆に等方性の特性を有するCNFをパネルとし、一体成形すれば理想的ですね。どちらの材料がいいということではなく、適材適所の発想です」
スポーツカーへの実装を皮切りに
自動車への実用本格化をめざす
自動車への実用本格化をめざす
影山教授が中心となって取り組んでいるエンジンフードのCNF化プロジェクトは、RTM技術を採用して試作され、低圧成形を可能にし、部品点数の少ない大型一体成形が可能であることを証明した。2018年には世界初となるCNFで試作したエンジンフードをトヨタ自動車のスポーツカー『TOYOTA 86』に実装。鋼製エンジンフードに比べて5割近い軽量化が実現可能であることを示している。
「エンジンフードは、耐デント性と呼ばれる変形を防ぐ強度が求められます。つまり、剛性が必要なのですが、その点CNFは期待にかなう素材であることは疑いないと思います。もう一点、エンジンフードには“歩行者保護”という重要な要素があります。万が一、事故で人と衝突した場合にエンジンフードで頭を強打する可能性があるからです。したがって、剛性が求められる一方で、人に損傷を与えるほど硬い物であってもいけない。衝突したら優しく壊れるくらいにしないとダメなので、そこは設計段階での工夫が必要です。ただ、あえて割れるようにしても、それが鋭利な割れ方であれば、破片でケガをするリスクがある。その点も考慮して、割れた場合に鋭利な形状にならず、なおかつ周囲に飛散しないようにしなくてはいけないのです。ほかにも、長期的な信頼性など課題点は多くあるのですが、金沢工業大学の各研究室の先生方とも連携し、一つずつクリアして、好感触をつかんでいます」
「エンジンフードは、耐デント性と呼ばれる変形を防ぐ強度が求められます。つまり、剛性が必要なのですが、その点CNFは期待にかなう素材であることは疑いないと思います。もう一点、エンジンフードには“歩行者保護”という重要な要素があります。万が一、事故で人と衝突した場合にエンジンフードで頭を強打する可能性があるからです。したがって、剛性が求められる一方で、人に損傷を与えるほど硬い物であってもいけない。衝突したら優しく壊れるくらいにしないとダメなので、そこは設計段階での工夫が必要です。ただ、あえて割れるようにしても、それが鋭利な割れ方であれば、破片でケガをするリスクがある。その点も考慮して、割れた場合に鋭利な形状にならず、なおかつ周囲に飛散しないようにしなくてはいけないのです。ほかにも、長期的な信頼性など課題点は多くあるのですが、金沢工業大学の各研究室の先生方とも連携し、一つずつクリアして、好感触をつかんでいます」
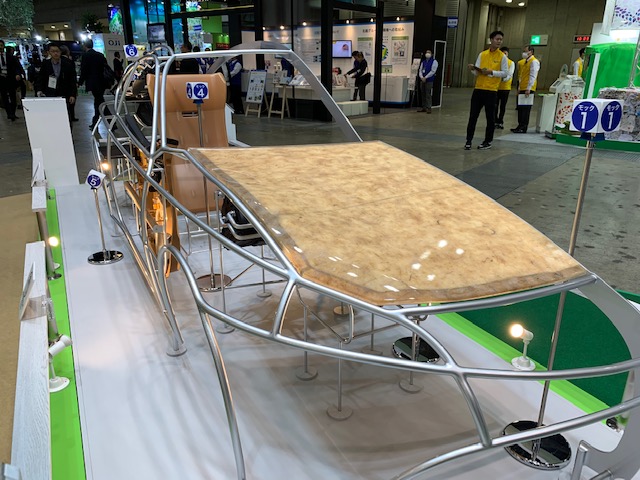
『TOYOTA 86』に実装したCNF製エンジンフード
CNFエンジンフードを実装した次世代自動車は、2035年の実用化をめざしている。ただ、内装材に関しては、早ければ2025年くらいには市販車に実装される可能性もあるという。
「長期的な信頼性を確保できれば、スムーズに進められると思いますね。あと、CNFは、極めて微細な繊維であるために、ほぼ透明に近い特性を持つのです。繊維が大きいために黒ずんで見えるカーボンファイバーなどとは対照的です。自動車は、ウインドウなど透明性が求められる部品も多いので、いずれはそちらにもCNFを活用できるかもしれません。また、タイヤにCNFを混入すると走行性能が向上することも判明しています。強度が増すことで、グリップ力がよくなるのです。タイヤメーカーでも研究が進んでいますね。
実はCNF自体は、自動車以外の分野ではすでに実用化されているのです。たとえば紙オムツです。CNFの吸水性に着目して開発されて商品化もされましたが、価格はやや高いようです。さらに、繊維の細かさを生かし、マスクにも使われています。こちらも高価なのですが、フィルター効果は段違いです。面白いところでは、ほんのわずかですが食品にも入っています。CNFをソフトクリームに少しだけ混ぜると、溶けにくくなるのです。最近では保湿性や保存性の点でどら焼き、また運動靴など多岐にわたって採用されてはじめています。そもそも世界で初めてCNFが実用化されたのはボールペンだったのです。インクの増粘剤として採用され、なめらかでかすれにくい書き味だと好評です。
CNFを研究して感じるのは、地球環境の保護という面で社会貢献ができるというやりがいが第一。また、私が過去に培ってきたCFRPの技術が応用できるという面白さがあります。トヨタ自動車に在籍していた頃から、軽量化が重要な課題で、材料一筋に研究・開発に従事してきました。特に航空宇宙分野の国家プロジェクトに約40年前にかかわったCFRPは印象深いです。当時のCFRPは自動車に使うなど、あり得ないほど高価でしたが、航空や宇宙分野の方々から学びながら、自動車への転用を考えていったのです。
その後、複合材料はリサイクルの時代となり、アルミが台頭します。私もCFRPと並行してアルミを学びました。2000年代には、トヨタ自動車のスーパーカー『レクサスLFA』の開発にも参加し、CFRPボデーを担当しました。10年がかりの一大プロジェクトでしたね。RTM成形技術をはじめ、当時の経験を最大限に生かしながら、現在はCNFに全力投球しているわけです。
「長期的な信頼性を確保できれば、スムーズに進められると思いますね。あと、CNFは、極めて微細な繊維であるために、ほぼ透明に近い特性を持つのです。繊維が大きいために黒ずんで見えるカーボンファイバーなどとは対照的です。自動車は、ウインドウなど透明性が求められる部品も多いので、いずれはそちらにもCNFを活用できるかもしれません。また、タイヤにCNFを混入すると走行性能が向上することも判明しています。強度が増すことで、グリップ力がよくなるのです。タイヤメーカーでも研究が進んでいますね。
実はCNF自体は、自動車以外の分野ではすでに実用化されているのです。たとえば紙オムツです。CNFの吸水性に着目して開発されて商品化もされましたが、価格はやや高いようです。さらに、繊維の細かさを生かし、マスクにも使われています。こちらも高価なのですが、フィルター効果は段違いです。面白いところでは、ほんのわずかですが食品にも入っています。CNFをソフトクリームに少しだけ混ぜると、溶けにくくなるのです。最近では保湿性や保存性の点でどら焼き、また運動靴など多岐にわたって採用されてはじめています。そもそも世界で初めてCNFが実用化されたのはボールペンだったのです。インクの増粘剤として採用され、なめらかでかすれにくい書き味だと好評です。
CNFを研究して感じるのは、地球環境の保護という面で社会貢献ができるというやりがいが第一。また、私が過去に培ってきたCFRPの技術が応用できるという面白さがあります。トヨタ自動車に在籍していた頃から、軽量化が重要な課題で、材料一筋に研究・開発に従事してきました。特に航空宇宙分野の国家プロジェクトに約40年前にかかわったCFRPは印象深いです。当時のCFRPは自動車に使うなど、あり得ないほど高価でしたが、航空や宇宙分野の方々から学びながら、自動車への転用を考えていったのです。
その後、複合材料はリサイクルの時代となり、アルミが台頭します。私もCFRPと並行してアルミを学びました。2000年代には、トヨタ自動車のスーパーカー『レクサスLFA』の開発にも参加し、CFRPボデーを担当しました。10年がかりの一大プロジェクトでしたね。RTM成形技術をはじめ、当時の経験を最大限に生かしながら、現在はCNFに全力投球しているわけです。
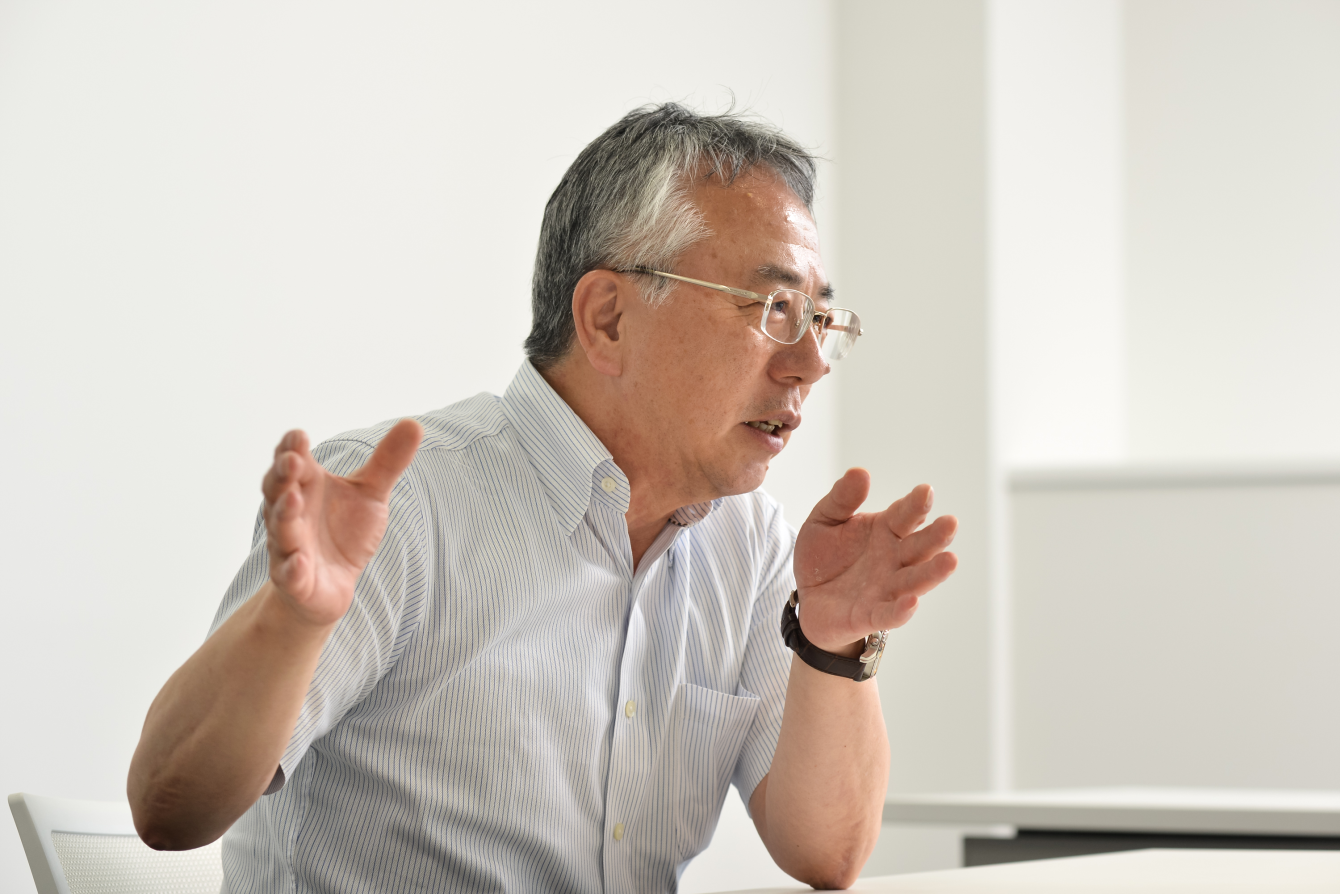
これからは、マルチマテリアルの時代だと言われます。鉄やアルミ、CFRPなどを含めた材料のコラボレーションがますます進んでいくでしょう。これまでずっと材料一筋にやってきましたが、材料がなければ何も作れません。動力性能向上や軽量化、あるいはCO2削減とか、どんな課題に対しても材料が大きなウェイトを占めます。将来に向けて、また新しい素材が生まれるかもしれないし、材料は必ず鍵を握るはず。最新の材料が出てきたとしても、過去の経験を生かすことが求められると思います。自動車の世界で貢献すると同時に、自動車で培ったものが他分野の産業にも展開できればうれしいですね。これからも、研究者としての自分の役割を果たしていきたいです」
自動車産業から地域、そして国へ
課題解決のカギは“戦略”にあり
課題解決のカギは“戦略”にあり
材料という分野にしっかりと軸足を置いて、日本の産業界を牽引してきた自動車業界の中核で活躍してきた影山教授だが、「自動車は、交通事故やCO2排出など、負の遺産も抱えている、そんな負の遺産を解決するためにも貢献していきたい」とも話す。自動車が抱える負の遺産を解決することは、そのまま日本という国が抱えている負の遺産を解消することにもつながるはずだ。高齢化社会しかり、環境問題しかりである。自動車産業は地域再生にも大きな役割を果たすだろう。
「日本のマイナス面を解消することが、必ず世界の課題解決にもつながる」と、影山教授の志は高い。最後に、卒業生にエールを贈ってくれた。
「ものづくりの醍醐味は“戦略”にある。いかにして早く、正確につくるか、課題をどう解決するのか、どう攻めていくか、それを考えることが面白いのです。私はどちらかと言えば、つくることより戦略を考えることが得意でした。金沢工業大学は、そんな戦略や企画に対して積極的で柔軟です。今回も学内外との連携に相当支援、協力いただいています。そんな大学で学んだ卒業生ですから、戦略への積極性・柔軟性をぜひ社会で生かしてほしいです」
「日本のマイナス面を解消することが、必ず世界の課題解決にもつながる」と、影山教授の志は高い。最後に、卒業生にエールを贈ってくれた。
「ものづくりの醍醐味は“戦略”にある。いかにして早く、正確につくるか、課題をどう解決するのか、どう攻めていくか、それを考えることが面白いのです。私はどちらかと言えば、つくることより戦略を考えることが得意でした。金沢工業大学は、そんな戦略や企画に対して積極的で柔軟です。今回も学内外との連携に相当支援、協力いただいています。そんな大学で学んだ卒業生ですから、戦略への積極性・柔軟性をぜひ社会で生かしてほしいです」
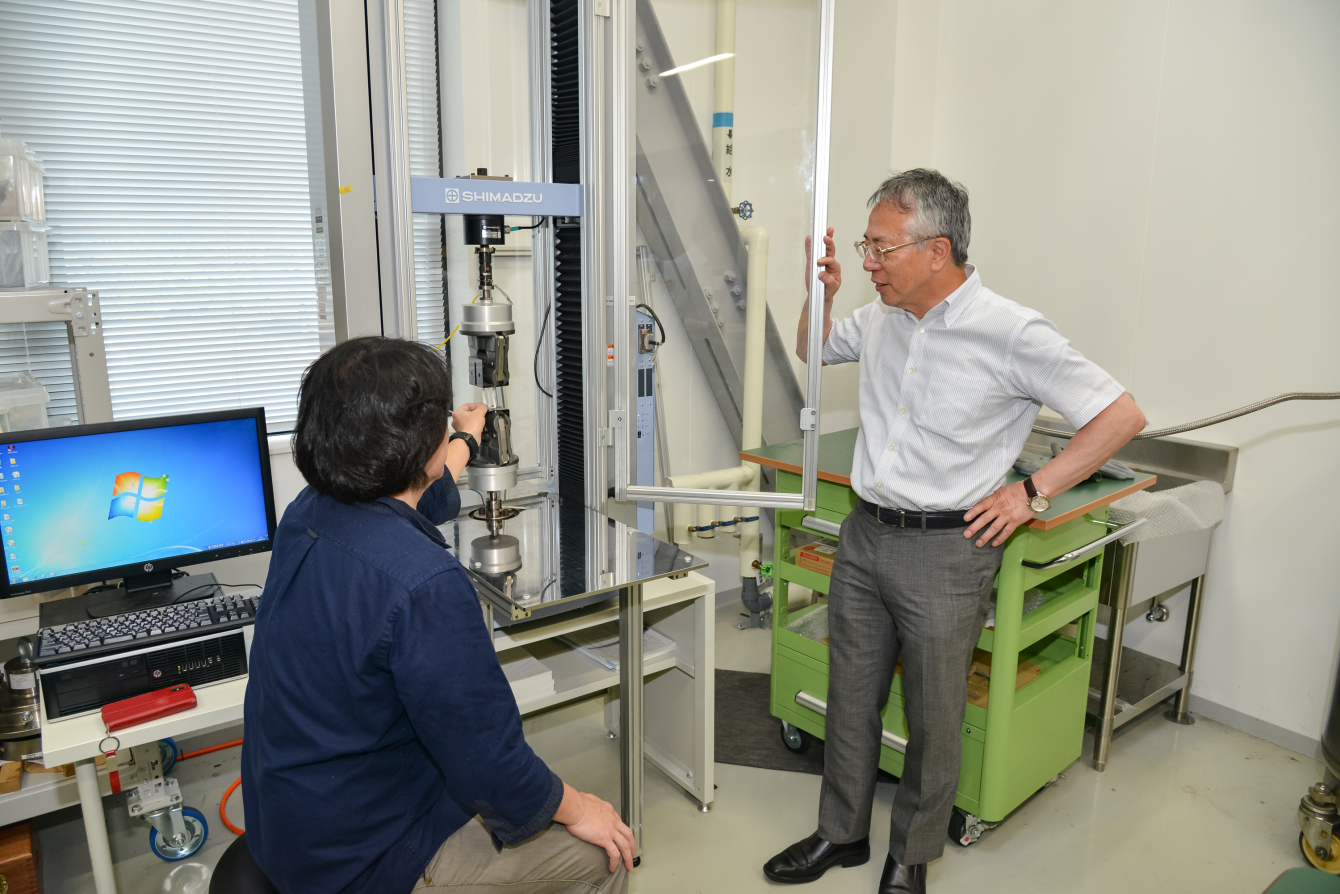
影山教授の研究室は東京・虎ノ門キャンパスにあるが、時折、白山市にある革新複合材料研究開発センター(ICC)を訪れ、研究・指導を行っている
前の記事
次の記事